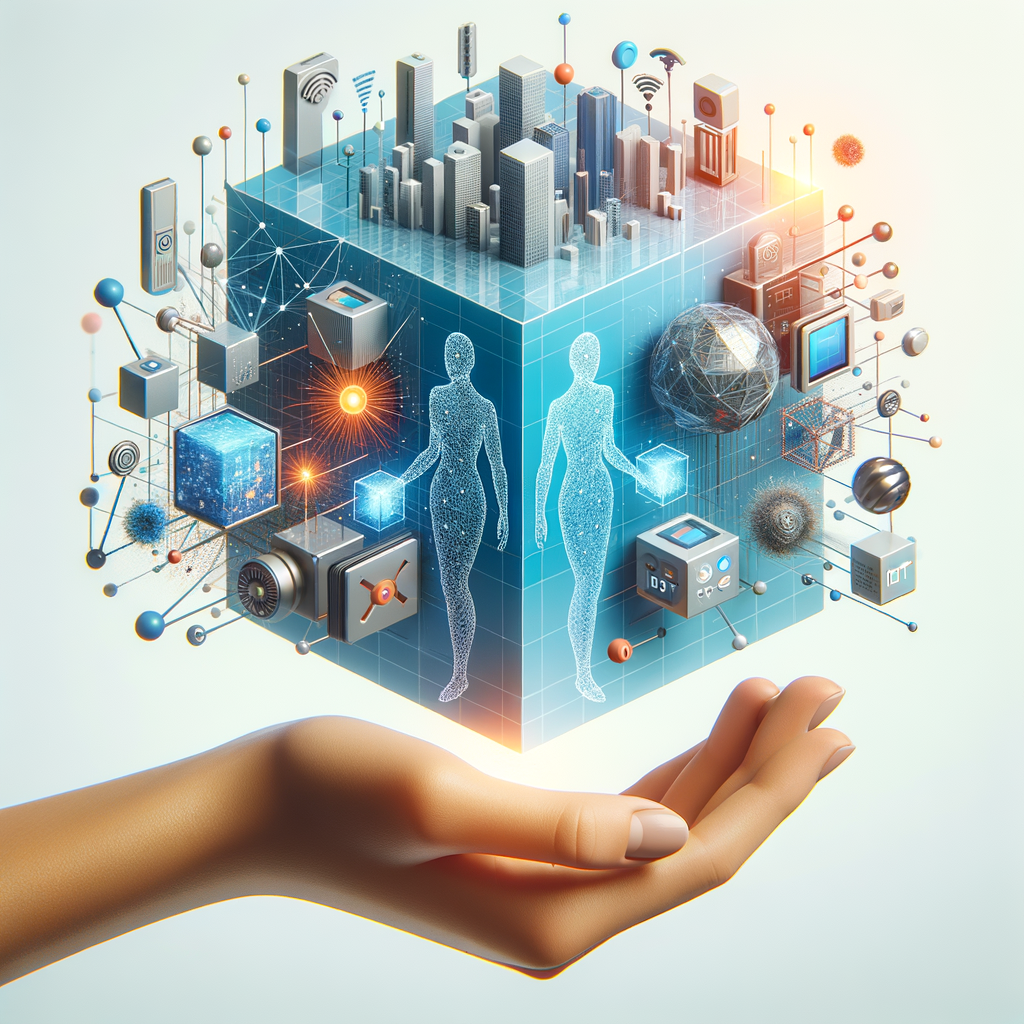
Unveiling the Future of Smart Manufacturing: AI-Driven Digital Twins and IoT
Explore how the convergence of AI, digital twins, and IoT is revolutionizing the manufacturing sector. This blog delves into the innovative impacts of these technologies, offering insights into improved efficiency, predictive maintenance, and real-time data analytics in industrial settings.
Unveiling the Future of Smart Manufacturing: AI-Driven Digital Twins and IoT
The manufacturing industry is undergoing a seismic shift towards digitalization, a trajectory marked by the integration of Artificial Intelligence (AI), the Internet of Things (IoT), and digital twin technology. This transformation not only promises to revolutionize operational efficiency but also ensures a seamless, connected industrial ecosystem capable of real-time data analysis and predictive capabilities.
Understanding Digital Twins
A digital twin is a virtual representation of a physical object or system across its various lifecycle phases. It uses real-time data and other sources to enable learning, reasoning, and dynamically recalibrating for improved decision-making processes. In essence, digital twins serve as living models, continuously updated with data from IoT devices and sensors embedded in physical assets. This symbiotic relationship offers a comprehensive view and understanding of how products behave under various conditions, ultimately guiding optimization processes in design, production, and operations.
IoT: The Backbone of Smart Manufacturing
IoT forms the backbone of smart manufacturing facilities, facilitating interconnected environments where every piece of equipment, process, and personnel are linked. This interconnectedness allows for the seamless flow of information and facilitates the coordination of all parts of the manufacturing process in real-time. By leveraging IoT, manufacturers can achieve significant gains in predictive maintenance, operational efficiency, and supply chain integration.
Key Benefits of IoT Integration
-
Predictive Maintenance: IoT sensors continuously gather data on machinery health, predicting failures before they happen. This proactive approach reduces downtime and maintenance costs significantly.
-
Energy Management: IoT-enabled devices provide insights into energy consumption trends, helping manufacturers to optimize energy use and reduce waste.
-
Operational Efficiency: By harnessing data-driven insights, manufacturers can streamline operations and improve resource allocation.
The Role of AI in Enhancing Digital Twins and IoT
AI enhances the capabilities of digital twins and IoT by providing sophisticated algorithms that process vast amounts of data to generate actionable insights. Machine learning techniques are applied to recognize patterns, predict future conditions, and optimize manufacturing processes and strategies.
AI Applications in Smart Manufacturing
-
Predictive Insights and Analytics: AI algorithms analyze past and present data to predict future operational scenarios, allowing for informed decision-making.
-
Robotic Process Automation (RPA): AI-driven automation in manufacturing processes accelerates production cycles and enhances precision, reducing human error.
-
Quality Control: By analyzing data from IoT sensors, AI can detect defects earlier in the production line, drastically improving quality control processes.
Real-world Applications and Case Studies
Numerous manufacturing giants are already reaping the benefits of integrating digital twins, IoT, and AI. Companies like Siemens and General Electric have adopted these technologies to enhance their digitalized production strategies, resulting in improved efficiency, reduced costs, and enhanced product lifecycles.
Case Study: Siemens
Siemens leverages digital twins for lifecycle assessment, allowing them to simulate product performance under different conditions, thus refining product quality and lowering operational risks. By integrating IoT and AI, Siemens achieves seamless interaction between all facets of the manufacturing process.
Challenges and Future Prospects
Despite the evident advantages, the integration of AI, digital twins, and IoT in manufacturing poses significant challenges, such as data privacy concerns, the need for robust cybersecurity protocols, and the vast initial investment required for technology deployment.
Future Trends
As technology continues to evolve, we can anticipate a more widely accessible smart manufacturing ecosystem. This will include developments in edge computing, enabling faster data processing and reduced latency, and the growth of AI-driven autonomous factories, which will further enhance the efficiency of supply chains globally.
Conclusion
The integration of AI, IoT, and digital twins is set to redefine the manufacturing landscape, offering unprecedented efficiencies and capabilities. By leveraging real-time data and machine learning, manufacturers can predict and respond to shifts in market demands promptly, ensuring sustainable growth and significant competitive advantages.
As industries continue to adopt these advanced technologies, the future of manufacturing looks promisingly smart, interconnected, and infinitely more capable of meeting the rapidly changing demands of global markets.